Technical Publication |
Information and Strategy for the
Facility Manager |
|
|
pdf Version
|
|
The Importance of Proper Cooling Systems Lay-Up
By Mario C. Uy
Introduction
Even the best program for preventing scale, corrosion, and fouling during the operation of the cooling systems can be wasted by improper shut down, improper lay-up, and improper maintenance on the cooling systems during downtime. Continued maintenance of the entire cooling system, even during shutdown, is essential in protecting it against corrosion.
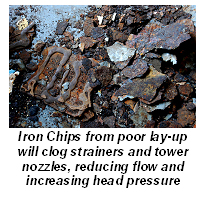
Open Loops
Open loops suffer corrosion when they are taken down improperly for winter lay-up. When the proper conditions exist, corrosion can continue to occur throughout the winter, developing iron chips that are common headaches during spring start-ups. Aside from the deterioration of the system, the iron chips can clog strainers and tower nozzles, reducing flow and increasing head pressure.
Open loops are commonly drained to protect them from freezing during the winter months. As the system is drained, it undergoes flash corrosion, a rapid oxidation process that occurs instantly when wet metal surface is exposed to air.
Even if the loops are drained, some water will remain in the system, corroding the metal surfaces during the lay-up period. Any residual water may also harbor bacterial growth, adding to the corrosion problems.
The above corrosion problems can be avoided by reducing any bacterial level and by adding a lay-up corrosion inhibitor prior to laying-up the open loops.
Chilled Loops
Chilled loops can also suffer corrosion during winter if they are not laid-up properly.
Presence of bacteria and/or insufficient corrosion inhibitor can accelerate corrosion during the winter lay-up, much like in the open loops.
The above corrosion problems can be avoided by reducing any existing bacteria and by maintaining proper level of corrosion inhibitor prior to laying-up the chilled loops.
In addition to corrosion, chilled loops are subject to freezing during the winter lay-up, especially the fan coils. Freeze protection must be taken into consideration to prevent a catastrophic failure.
To prevent freezing, many engineers add glycol-based anti-freeze. The anti-freeze can be added permanently into the loops; or it can be flushed through the coils or simply left in the coils.
The amount of glycol to be used is a balancing act. Too much glycol reduces the efficiency unnecessarily. Too little glycol may become a nutrient for any residual bacteria in the loop. This is especially a problem when glycol is added to the coils only. Very often, the coils are placed back in service without flushing the glycol out, leaving a small amount of glycol in the loop. In large quantity, glycol can deter bacterial growth, but in small quantity, it becomes a nutrient for bacteria. This problem can be prevented by using a non-glycol based anti-freeze.
Before draining the chilled loops with anti-freeze, check with your local sanitary district regarding its regulations on the discharge of anti-freeze into the sanitary sewer.
September 2009
|